Use Heatmaps to Fix Broken Processes
- 22 March 2025
- Posted by: Rob
- Categories: Data Engineering & Analytics, Quick Thoughts
No Comments
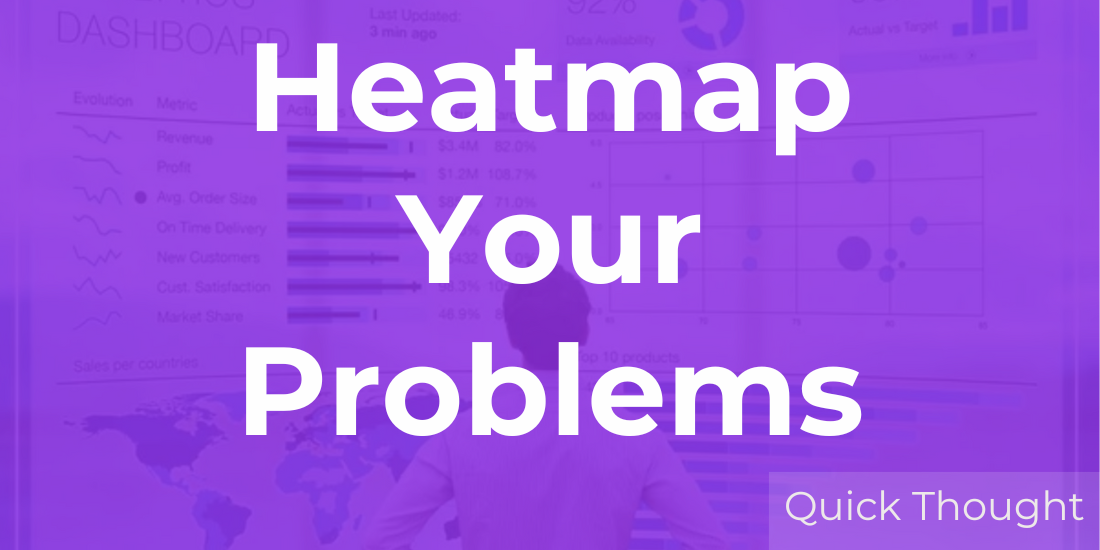
You’re collecting data—but are you using it to find what’s broken?
One of the most underrated tools in wholesale analytics is the heatmap. Whether it’s tracking picker movement, order issues, or customer support queries, heatmaps help you visualise where things are going wrong.
Examples that work:
- Warehouse heatmaps to show where pickers spend the most time (or backtrack the most).
- Product heatmaps to highlight high-return or slow-moving SKUs.
- Customer support heatmaps to reveal what days and times issues spike.
- Website click heatmaps to find what content draws attention—and what gets ignored.
The beauty of a heatmap is how quickly it shows concentration of activity. You don’t need to trawl through rows of data—it jumps off the screen.
And once you see it? You can act:
- Move high-frequency SKUs closer together
- Review layout and walk routes
- Spot training gaps based on error hotspots
- Optimise pick paths or support cover times
If you want to improve efficiency, start with a visual. Because when you can see the pain points clearly, the fixes become obvious.
Don’t just report the data—map it.